Last Updated on August 4, 2021 by PALFINGER
What does one do when customers can, from one day to the next, no longer attend a Factory Acceptance Test (FAT) in person? A step, which is so essential in completing business projects. This is a question one would not have dreamed to ask before the coronavirus pandemic. The solution was found in-house in a remote device that was already widely used within the PALFINGER Group before the crisis and has become even more important in recent months: the PALFINGER Smart Eye. Iavor Markov, Contract and Tender Manager for Marine and Wind Cranes at PALFINGER, and his colleagues swiftly adapted this innovative technology for remote FATs.
We sat down with Iavor to talk about this new way of conducting FATs in his particular field of expertise at PALFINGER, what advantages and challenges it comes with, how customers have reacted to it, and what the future holds. Iavor, let’s start at the beginning …
What was the status quo regarding Factory Acceptance Tests in your area of responsibility before the pandemic?
In the offshore wind business, cranes are presented to customers or third parties, such as surveyors, before final approval. This is the primary purpose of the so-called FAT, which usually takes place at our PALFINGER manufacturing site in Maribor, Slovenia. During these tests, the customers familiarize themselves with the crane. They get a chance to assess its quality, functionality, and operability. Furthermore, the FATs are an excellent opportunity to introduce customers to crane features they might not yet be aware of. These tests are highly complex, crucial events that tend to involve people from all around the globe.
Which challenges are customers facing?
Lockdowns, closed borders, and travel restrictions resulting from the coronavirus pandemic have made it impossible to schedule face-to-face FATs in Maribor. We had to ask ourselves how we could proceed with the tests regardless. It is, after all, imperative to avoid month-long delays of major – and very expensive – orders such as, in our case, big offshore wind farm projects.
What solution have you ultimately come up with?
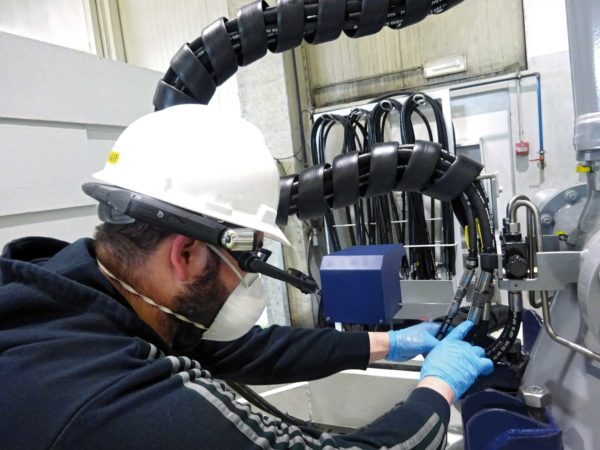
The project manager wearing the device films all steps, enabling the customers to follow the process on their screens.
Some of our service colleagues based in the Netherlands recommended an efficient in-house solution for conducting remote FATs: the PALFINGER Smart Eye. This wearable remote device in the form of a helmet, featuring a flexible and movable camera, offers excellent sound quality to ensure two-way communication. It solves several problems at once. The project manager wearing the device films all steps, enabling the customers to follow the process on their screens. He can also zoom in on certain individual sections whenever questions arise. Furthermore, the transmission quality is significantly higher due to the fact that one no longer needs to remain glued to smart phones or fixed cameras for hours. This guarantees efficient communication with less interruptions.
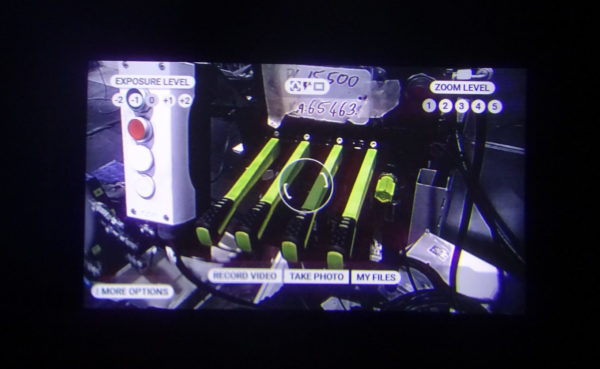
PALFINGER Smart Eye vision: The project manager wearing the device can zoom in on certain individual sections.
The project manager can capture images of specific details for the customers, who can highlight sections of specific interest.
Last but not least, using the PALFINGER Smart Eye allows more people than usual to take part in the FATs. In fact, my personal record of participants for a remote FAT stands at almost 20. Normally, only one to five participants on the customer side take part in the face-to-face procedure.
What advantages does the PALFINGER Smart Eye bring for both the customer and for PALFINGER?
The main purpose of the FATs is to answer questions and solve problems on the spot. While this was already a major aspect of face-to-face FATs, the remote tests now include more people with very different viewpoints. The result is that more questions are asked and answered upfront. Consequently, this allows us to consider a broader range of customer wishes during the process. Quality issues and customer requests can be recorded and addressed in advance without the need for additional tests and measurements. This ultimately saves time and money for both the customers and PALFINGER. Another advantage that should not be underestimated, especially in the current environment, is that remote FATs significantly reduce the need for travelling.
What challenges do you come across when using the Smart Eye solution?
One rather challenging aspect is that conducting FATs via the PALFINGER Smart Eye feels quite different, as your audience is merely following the day-long process on screens. You need to find a proper way to engage with the viewers and, at the same time, remain focused and on point.
There is, however, one element that even interactive technology like the PALFINGER Smart Eye cannot replace: the human element. We usually get a chance to become acquainted with customers in a more informal setting during coffee breaks or business lunches. The coronavirus pandemic has robbed us of this pleasure for now. A personal relationship built on trust remains vital, especially in a project defined by high order volumes.
You are an expert in this particular field. What does the future hold?
Personally, I believe that a hybrid solution would be most efficient for both the customers and PALFINGER. It would combine the best of both worlds by allowing a couple of people to follow the FAT on-site while also making it available remotely to a broader audience.
How has the customer feedback been so far?
As with all new technologies, customers seemed a little skeptical at first. However, this initial skepticism soon turned into enthusiasm and excitement. The feedback regarding the remote FAT itself, as well as the customer proximity it offers, was overwhelmingly positive. Customers were particularly amazed by the quality and professionalism of the solution, which suggests that we could be one of the few players offering such an option. In fact, customers are already asking whether they could purchase the technology from PALFINGER. That is the highest compliment one can receive.
That sounds great. Can you give us an example?
Only recently we handed over two cable deck cranes for the Greater Changhua offshore wind farm in Taiwan. The client could not travel due to restrictions, so we used the PALFINGER Smart Eye as described. We were in Maribor, and the client’s representatives sat in Singapore and Denmark. I wore the device, while two colleagues conducted the FAT. Everything went smoothly and our customer echoed the highly positive feedback we have received from other clients.
I have personally been involved in 16 remote FATs, attended by a total of approximately 150 people from 12 countries, since the first lockdown. In many cases, the remote tests were decisive for the approval of countless other cranes. I am very proud of our innovative FAT approach involving the PALFINGER Smart Eye solution. It once again shows that we have a lot of creative minds in the organization, who never cease to impress us as well as our customers with sophisticated concepts, ideas, and solutions – particularly for challenges as such, and even more so in difficult times like these. Be that as it may, I am nevertheless really looking forward to being able to meet our clients in person again – hopefully sooner rather than later.
For more information about the PALFINGER Smart Eye, check out the following video: